Please note
that I've written some additions and revisions
to this Guide.
There are a number of ways to make a good working reed for any
particular chanter. The following is the method that I find works
best for my chanters.
LIST OF TOOLS AND MATERIALS
(For sources, see end of guide)
BENCH VISE
METAL SHEARS
METAL FILE
UTILITY KNIFE
CALIPERS
STAPLE ROLLING / EYE FORMING MANDREL (dimensions
given at end of guide)
SHOOTING BLOCK (dimensions given at
end of guide)
HARDWOOD CHOPPING BLOCK
SANDING CYLINDER(S)
COPPER SHEET (.018-.020 thickness)
SANDPAPER (240, 320 grit)
CANE TUBES (arundo donax)
INCANNEL GOUGE (ground on inside of curve)
FINE TOOTHED DOVETAIL SAW
DENTAL FLOSS
COBBLER'S THERMO WAX AND BEES WAX
PLUMBERS TEFLON TAPE
MAKING THE STAPLE
I use a rolled staple for both the concert pitch D and the flat
pitch B and C chanters. I find that standard tubing staples produce
a reed that has the octaves out of tune with each other. 3/16"
outside diameter brass tubing does get fairly close to the tuning
that is desired for the D chanter, and can be used when starting
to make reeds. 5/32 OD tubing will ork fairly well for the B &
C chanters.
To make a rolled staple start by cutting a trapezoid slightly
larger than the desired size out of .020" copper sheet.
For D Chanter: For
C Chanter:
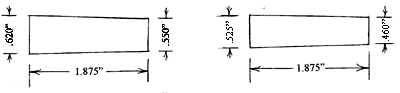
CORRECTED END MEASUREMENTS: D Chanter--.620 and .550 For C Chanter--
.525 and .460.
Place the staple blank in a bench vise and file one edge. You
can check the evenness of the edge by placing it against a metal
straightedge or the back of your calipers, and holding it up to
the light. When that side is sufficiently straight file the other
side to the desired width, and check it for straightness.
Begin rolling the blank by placing it on the top of the vise
jaws which are open about 1/4" or so. Place the tapered
rolling mandrel (a steel rod turned or filed to the inside
shape of the staple) on top of the copper blank and gently tap
the mandrel with a hammer to bend the copper in the middle.
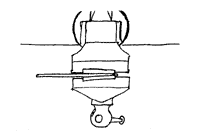 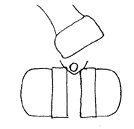
Then place the bent staple blank and mandrel on a hard surface
and hammer the copper around the mandrel. Try to get the staple
as round as possible when viewed from the ends. For the D chanter,
the rolled staple should now have an inside diameter of .175"
at the bottom end and about .150" at the top.
When the staple is round it is time to shape the eye at the narrower
end. If you are making a tubing staple start here after cutting
it to length (a plumbing tubing cutter works well). For this operation
you will need a second mandrel, one that has been filed into the
eye shape. You can combine these two functions in one tool, by
tapering both ends of a steel rod and filing one end into the
eye shape (see dimensional drawing at end
of guide).

Place the mandrel up into the staple and gently hammer the top
into the desired eye shape. Taper this squashed area back to about
halfway from the top end.
The narrow inside diameter of the inside of the eye for the D
staple should be .065", and .050" for the C.
File the outside of the eye to clarify the eye shape and along
the seam to make it smooth. Deburr the openings carefully with
a utility knife.
THE CANE SLIP
A cane tube diameter of about 1" to 1.050" works best
for the D chanter reed and 7/8"(.875) does well for the C
and B pitched reed.
Final slip dimensions are as follows:
Concert D pitch:
[dimension at end is .500", entire length for D, C and
B is 4.5"]
C and B pitch:
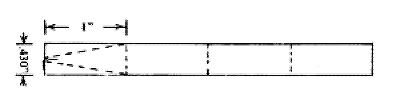
[dimension at end is .430"]
To form the slip, first cut a tube of cane to length. I place
the cane against the back of the shooting block
and slowly cut it with a fine toothed dovetail saw. Then slice
a piece from the tube about .040" wider than the final width.
Place it on the shooting block with the bark face down and gouge
the inside until the surface is flat:
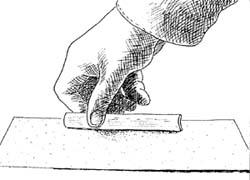
Take the slip and sand one edge straight on a flat surface (240
grit works well). Check for straightness against a straightedge
held up to the light. When you find a bump hold the slip above
it and sand gently. Slight pressure should cause the bump to sand
down.
When one side is flat, sand the other until the target width
is reached for the length of the slip.
The slip can now be final-gouged, getting it as close to the
finished shape as we dare. Gouging saves time versus sanding on
the sanding cylinder, but gouging too deep makes it impossible
to clean up and smooth the inside surface. As a rough guide, gouge
the edges to twice the ultimate thickness, and put a slight curve
into the center:
Finishing the slip requires a round sanding block. I find that
a 2.25-2.50" OD PVC pipe section works well for the D reed
and a 1.8" diameter works nicely for the C. Depending on
the hardness of the cane and other variables, different sized
sanding cylinders may work better. It is important to keep the
desired end result in mind and use whatever means best achieves
this. The goal is that when the outside of the reed is sanded
and scraped, the lips will be open just slightly more than the
optimal width. The bridle can then be used to bring the reed lips
together the necessary amount.
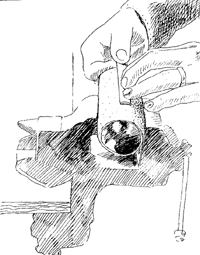
To finish the inside of the cane slip, wrap some fast cutting
sandpaper (150 grit) around the sanding block and place it in
the vise. Holding the slip between the thumb and first two fingers
of the right hand sand first one end then the other, applying
pressure with the fingertips of the left hand. Sand until the
inside is smooth, and the edges are uniform. The goal on the edges
is not knife sharp, but a few thousands of an inch thick (the
thickness of two or three sheets of paper). A thick edge will
produce a dull sounding reed. Finish sand the same way with finer
paper (280 grit).
FORMING THE REED HEAD
Take the smooth, straight slip and mark a center line and guide
lines 1 1/8" from either end. Also mark the center of each
end and draw connecting line to the edges of the 1 1/8" lines.
This is a rough guide to trim the tails of the reed. With a sharp
utility knife trim the tails leaving a width of about 1/8"
at either end.

Now score the center line, drawing the knife from the outside
edge to the center of the slip. Flip the cane around and repeat
the cut on the other side. It is important to make this cut in
two steps, if you try to cut from one edge to the other in one
move the cane will splinter. Put the scored cane bark-side up
on the sanding block and cut straight down at the center line.
The score cut on the inside of the slip should help make this
fairly easy.
Tie these two sides together using thermo-waxed floss or hemp,
making sure the edges are parallel and not overlapping. Leave
about 1.5" from the tip of the tails unwrapped for sanding
the edges. The reed head can be finish profiled by either sanding
the edges into symmetrical curves tapering up to the wrapping:

or into the trickier bottleneck design:
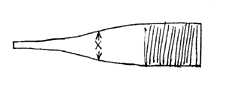
It requires some additional paring with the utility knife to
get the shape right, and some finish sanding of the edges to smooth
them out and taper them towards the wrapping. As a guide, width
X should be around .400" for the concert pitch reed and .335"
for the C pitch reed.
Chamfer the edges of the tails below the 1" point. Pipemaker
Kirk Lynch suggests removing much of the bark below this point,
especially with very hard cane, to reduce the chances of splitting.
When the reed head is shaped mark a line 1" from the tail
end, and slide it 7/8" onto the staple. Wrap some Teflon
tape around the staple and cane up to the 1" line. This helps
seal the edges of the cane and the seam of the staple.
For wrapping the reed I use the heaviest unwaxed dental floss
I can find. I wax a 6' length of it with a 50/50 mixture of bees
wax and cobbler's thermo wax. The bees wax makes the sticky cobblers
wax easier to work. Pre-waxed floss will also work if the Teflon
tape is used with it.
Tie the floss onto the bottom of the the staple about 3/16"
from the end, and, holding the reed in the eye-shaped mandrel,
wrap upwards. As you get to the top of the staple the edges will
begin to close. Keep wrapping until they do. This should happen
at about the 1" line. Then wrap back towards the bottom and
tie off. The binding hemp can now be removed.
SCRAPING THE REED
The reed is now tied up and needs to be scraped. You can either
go directly to sanding the faces on rough paper (120/150 grit)
or first pair them with the utility knife into a rough V shape.
Be very careful at this point, too much pressure on the thick
edges can crack them. As they get thinner they flex more easily.
With the gentle pressure of the first finger on the back of the
cane head, sand slowly back and forth, first one side then the
other, until they both develop a v-shaped sanded area. Continue
sanding until the tips get fairly but uniformly thin. Then chop
the reed edge back about 1/16" to clean it up with one downward
press. The sanded area or "scrape" should look like
this:
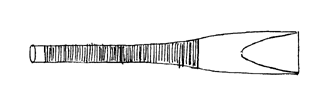
Test the reed for a crow sound by sucking sharply through the
staple end. With the edges thin it should sound. If it doesn't
then the lips are probably too far apart or too stiff, and additional
scraping may be necessary.
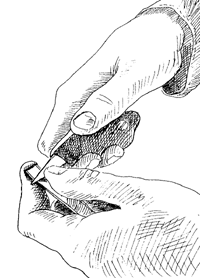
At this point, actually scraping the cane works best for accuracy
in thinning the blades in the desired area. In this case that
might mean lengthening the V-scrape and leaving the edges alone.
With the utility knife or an Opinel knife scrape from the bottom
of the V out towards the edge. Support the blades of the reed
underneath with the first finger of the left hand, and guide the
knife from behind with the left thumb. Scrape until the crow sounds.
At this point let the reed rest for a few days (if you can) before
attaching the copper bridle.
The bridle is a 1/8" wide copper strip that can help either
open or close the reed and is essential for the fine adjustment
of the reed. To fit a bridle to a reed first form one side of
the strip with needle-nosed pliers, then fold the other side by
hand around the edge of the reed (fig.1). Adjust the bridle carefully
with the same pliers.
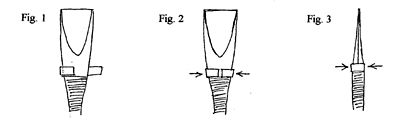
To open the lips of the reed squeeze gently at the corners of
the bridle with the pliers (fig. 2). To close them gently squeeze
the front and back of the reed together at the bridle (fig.3).
This is the spot where the reed is most sensitive to cracking,
so don't attempt to close the reed more than it wants to, and
try to do it with your fingers before using the the pliers. In
the event that you can't get the reed closed enough, you might
want to consider using a larger diameter sanding tube next time.
To get the reed working well in the chanter will take some experimentation
and can sometimes only be achieved by trial and error. The following
dimensions should help in deciding how far back to chop the edges
and how much to scrape. Note that the length of scrape will vary
from one reed to another and that dimensions of it are meant as
a rough guide. The length of the D reed, from bridle to tip, may
be shorter than .930", but no less than .875".
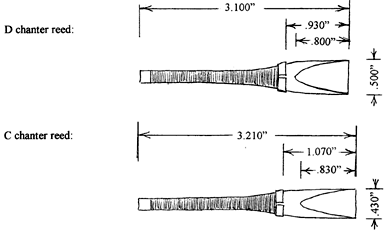
ADJUSTING THE REED AND TROUBLESHOOTING
Different chanters have their own particular idiosyncrasies to
keep in mind when making a reed for them. The following are some
that relate especially to my chanters.
Concerning the concert pitch D chanter: The note to watch, or
actually listen for, is the second octave E. How this note sounds
will tell nearly all on how far open lips of the reed should be.
And as you will surely find out, a little difference in the aperture
makes a great difference in the sound. If this note is very sharp,
approaching F natural, or so unstable that a little pressure causes
it to go sharp, then the lips need to be opened. The optimal aperture
is the minimum that produces the slightly flat second octave E.
If the lips are too open the sound will be too loud, harsh, flat
pitch-wise, and hard to blow.
Concerning the flat C chanter: The note to watch is the bottom
D. If the reed is too short, or scraped too much, the bottom D
has a tendency to gurgle.
Concerning chanters in general: Quite often the bottom hard D
will need to be tuned. To get it in tune with the rest of the
chanter a twist tie or some such object can be inserted into the
bell of the chanter. The larger the object in the bell the flatter
the hard D produced and the easier it is to sound.
DIRECTORY OF TOOLS AND MATERIALS
I now carry some reedmaking supplies including a Basic
Reedmaking Kit.
Your local hardware store or lumberyard should have the following
items:
BENCH VISE with at least a 2" opening
METAL SHEARS, I use the yellow handled straight cutting Wiss brand
shears
METAL FILE, I use a standard Nicholson mill bastard file
UTILITY KNIFE
OPINEL KNIFE (optional for scraping)
SANDPAPER of varying degrees of roughness
PLUMBERS TEFLON TAPE
FINE-TOOTHED DOVETAIL SAW
COPPER ROOF FLASHING .018-.022" (that's thousandths)
CALIPERS can be obtained cheaply from: Enco Manufacturing, 5000
w. Bloomingdale Ave., Chicago, IL 60639-4587. Their telephone
number is (800)873-3626. They have an import 0-6" dial caliper
for under $25, model 610-5026.
Woodworker's Supply, 1108 North Glenn Rd., Casper, Wyoming 82601,
telephone (800)645-9292, carries BENCH VISES. They have several
models, including model# 891-567, a portable vise with 2 1/2"
jaw opening, that sells for under $20.
TUBES OF CANE, GOUGES, WAX, SANDING CYLINDERS and many other
reedmaking supplies can be ordered through Nick
Whitmer or David Keenan at Celtic
Fire, Ltd., P.O. Box 1294, Forestdale, MA 02644-1294 Telephone
is (508)833-3724. You can also get a nice gouge from Garrett Wade
Company in New York, (800) 221-2942. Ask for the 3/4 inch scribing
gouge. Na Piobairi Uilleann also sells gouges and reed-making
supplies.
If you want to order CANE from the source, Espana, Medir
S. L. is the company. Tell them how many kilos you want
(I would suggest at least 2 kg to make the custom duties you will
have to pay worthwhile), the diameters that you want (e.g. .925
inch or the metric equivalent 23 to 24mm) and that the cane is
for the Irish Uilleann pipes. Their address is: Medir S.L., Paratge
Balitra s/n- Apartat 108, 17230, Palamos [Girona] Telephone 972/
31 43 39, Fax 972/ 31 89 17
RESOURCES
David Quinn's The Piper's Despair is a fine book on reedmaking
for the Northumbrian and Uilleann pipes. They are $15 per copy,
checks made payable to D. M. Quinn and the address is Koehler
and Quinn, 70 Markham Road, East Montpelier, VT 05651
Iris na bPiobairi The Pipers' Review, published quarterly
by the Irish
Pipers Club, has many articles pertaining to reedmaking, and
if you play the Uilleann pipes you should be a member of the Pipers
club anyway. Yearly subscription and membership is U.S.: $15,
Canada $19 and foreign $22. Their address is PO Box 31183, Seattle,
WA 98103-1183. Telephone: (206)784-7353.
NA Piobairi Uilleann also has a journal, An Piobaire,
a website, and many books, tapes,
and supplies for sale. Their address is 15 Henrietta Street, Dublin
1, Ireland. Phone: 353 1 873 0093, and E-mail npupipes@iol.ie.
Both these Pipers Clubs have websites, they're listed on our
links page.
DIMENSIONS FOR SHOOTING BLOCK AND STAPLE-FORMING
MANDREL
For making the shooting block I use 3/4" thick oak, but
any hardwood of similar thickness should work well. Glue and screw
the pieces together, and then mark two parallel guide lines .600"
apart down the top face. Carefully gouge between the lines to
form a channel to comfortably hold the cane slip. I then add dimensional
guides of .875", 1.000", and 1.125" on the edge
of the top surface, for quickly marking the slip and the the staple.
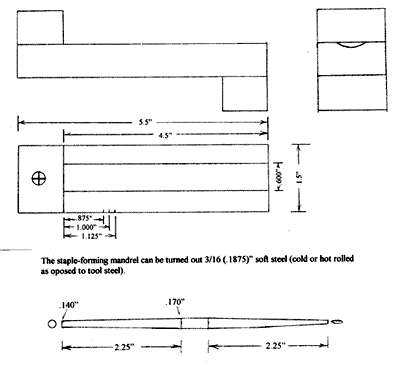
Please note: I guarantee my reeds for at least the first three
months barring any scraping, sanding, or spindling (not to mention
folding or mutilating) on your part.
TROUBLESHOOTING
CHART |
Problem |
Possible cause and/or remedy |
back D weak |
lips too thin, or too closed--chop edge back or open with
bridle |
high E is sharp |
lips too closed, or not vibrating freely enough--open with
bridle or scrape more |
gurgle on bottom D |
reed too short, or scraped too much |
reed is dull sounding |
blade edges too thick--untie and resand on cylinder |
reed requires much pressure to play |
lips too open, or cane too stiff--close with bridle, may
require more scraping |
hard D difficult to sound |
bottom of V needs more scraping, possibly into U-shape |
back D is sharp |
D-hole needs to be closed with tape, sanding the lips will
also flatten the back D |
back D is flat |
reed needs to be shortened--chop the edge back a bit, or
insert rush to flatten notes below the back D |
second octave is too sharp |
staple size [internal volume, not length] needs to be reduced |
second octave is too flat |
staple size needs to be increased |
second octave is difficult to obtain |
blades too open, too thick or too long --close with bridle
or scrape more |
high B is difficult to obtain |
blades too short; staple volume too small; volume of chanter
from thumb-hole to throat too big for reed--try wire rush
in this area or staple with larger internal volume. |
________________________________________________________________
Reedmaking Guide - Revisions and Additions
I originaly wrote my "Reedmaking Workshop" guide in 1997 and
my basic approach has stayed as it is described in it. I have
made some minor, but none the less noteworthy, adjustments to
it, and continue to experiment with the various variables involved
in order to produce the most consistent positive results. As in
the original guide I thank Benedict Kohler for his help as trouble-shooter
par-excellence.
Revisions April 2001
- Opening Bridle Vs. Closing Bridle - I now aim to use
the bridle to open the reed slightly. This relieves some of
the pressure along the edges and will hopefully lead to the
reed maintaining a nice shape over time. One side effect could
be a weaker back D; pressure along the sides ensures the edges
seal, if there is too little pressure leaks can occur that weaken
the back D.
- Staple Eye Opening - See revisions Jan. 2004
- Cane Tube Size- See revisions Jan. 2004
- Shape of the Reed Head- I am now most often using a
straight-taper-with-gentle-outside-curve design for the shape
of the reed head, as opposed to the "bottle-neck" shape. The
straight-taper shape is easier to get symetrical, and conducive
to a longer gradual taper towards the top of the reed head.
Staight parallel sides can have a tendency to leak and cause
a weak back D note. I try to keep the taper as long as possible,
at least up to .5" from the top of the the reed. Therefor, when
I temporarily wrap the reed-head for shaping I wrap less than
.5" to allow sanding of the edges up to this point. This taper
has a gentle outside curve to it should blend invisibly into
the parallel part under the temporary wrapping.
________________________________________________________________
Revisions January 2004
- Staple Size and Eye Opening.
I am currently using a D-pitch staple that in its unrolled form
is .550" at the top and .620" at the bottom. It is
a bit bigger than what I had been doing but works very well
for me now.
Slightly different reed styles (wider/narrower head, longer/shorter
blades) may require different sized staples. The best way
to figure out what works best for you is to make a staple
and a reed and check the octaves. If the second octave is
sharp then reduce the size of the staple and vice versa.
As for the eye opening I am generally using .065" for
the D chanter staple.
Flat Chanters: For the C reed I now mostly use a staple
bland size of around .460" at the top and .525"
at the bottom. The length is still around 1.875" long.
For the B reed the staple blank is .445" at the top
and .500" at the bottom. The length is around 1.950"
long. The inside eye opening for both the C and B staples measures
around .050".
aedfs
- Cane Tube Size. I now use tubes of cane 1.025"
to 1.050" diameter for the D chanter reed and .825-.875"
diameter for the B and C chanter reeds.
- Sanding Tube Size. I am currently using sanding cylinders
ranging from 2.5" to 2.7" for the D chanter reed and
1.825 to 2.00" for the B and C chanter reeds.
- Trouble Shooting Whereas the difficult to sustain 2nd
octave B used to show up fairly regularly, the larger staple
size I now use has eliminated this problem. Occasionally an
unstable second octave E will appear, see the trouble-shooting
guide for remedies, but also consider sending your Gallagher
chanter in for a bore adjustment if it was made before 2004
(before chanter #260). The process is quick and painless and
improves the general performance of the chanter.
Additional Information
Thickness of cane slip- the thickness of the finished
slip can be a usefull but not essential measurement to the reed-making
process. The thickness is determined by 1. the arc of the outside
of the cane (from the shape and diameter of the cane tube), 2.
the width of the cane slip, and 3. the arc created by the sanding
cylander. I like this measurement to be in the .040-.050" range
for a D reed, but I suggest not letting this measurement determine
how you finish the reed. Instead let it be one piece of information
among many that helps you troubleshoot problems. An example of
using it as an aid would be in a situation where a newly made
reed that is shut closed. Trying to force the lips apart with
a bridle causes the edges to separate, a thus reveals that there
is not enough arc in the blades. This means that a smaller sanding
cylander is needed. If the slip was on the thinner side before
scraping, say .035-.040, a smaller sanding tube may cause a similar
piece of cane to be too thin when sanded. One solution would be
to use a smaller diameter of cane, and a smaller sanding cylander.
Bridle Placement Options- I normally place
the bridle imediately above the waxed-hemp wrapping. Sometimes
other placements work better. If a reed needs to opened up, placing
the bridle 5/16 or so above the wrapping is a good option to consider.
Experiment and find what works best.
[ Uilleann.Com Home | Price List and Ordering Information | Flutes Information and Price List | Photos and Music Clips | Other Products: Tutors and Accessories | About the Maker | The Reed-Making Workshop | NEW Photo Page | Maintenance Guide | Uilleann Piping Contacts | Frequently Asked Questions | Uilleann Piping Links | Jerry O'Sullivan's Website | Contact Information | Tionol Information Page ]
©1997—2012 Seth Gallagher
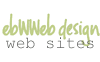
please
report any problems to the webmaster
|